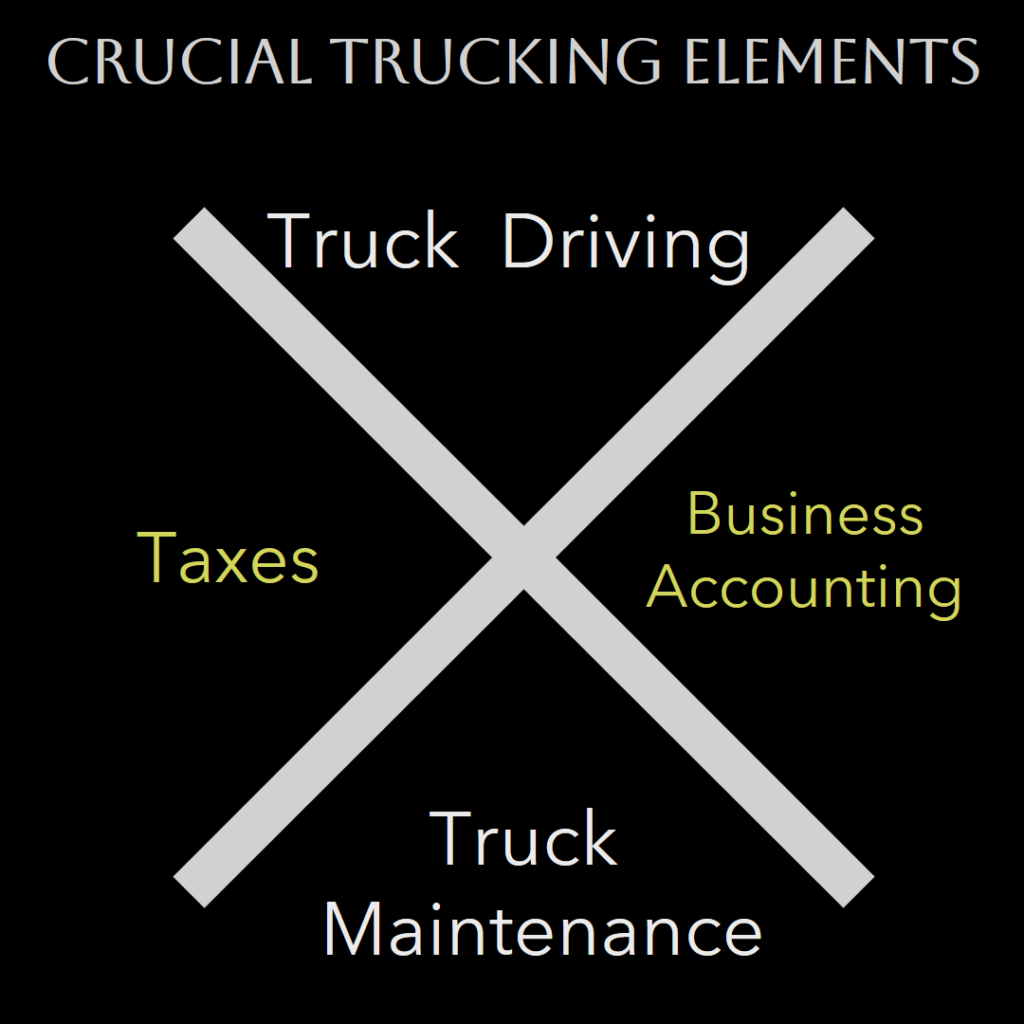
Introduction
For those embarking on the exciting journey of obtaining their own authority (or what I like to call ‘Freedom authority’) in the trucking industry, this blog post serves as a compass, guiding you through the essential skills needed to drive while running your own business from the road. I believe there to be five essential elements and even though my philosophy is that trucking is only a great job to the extent it can be done healthily, I will leave out the fifth element for now (health and fitness) and focus only on the first four: driving the truck, maintaining the truck, business accounting, and taxes.
Element One: Learn to Be a Truck Driver
When I first started trucking, I drove for Knight Transportation for a year and a half as a company driver. I absolutely loved every part of it. I received my CDL after attending Knight Transporation’s truck driving school in Phoenix. Next, I drove with a trainer for a month and after that, was issued a truck and I hit the road on my own. After a decade confined to a government cubicle, I absolutely loved the freedom and the adventure of trucking. It was during this year and a half that I learned the first, and most important pillar of trucking profitably–driving the truck. Here are some of the aspects of truck driving I learned.
Learning to navigate the U.S. Highway system
Navigating the vast network of highways became an intriguing revelation for me. Before I started trucking, I had no idea that the highway numbers had a deeper meaning. The U.S. highway numbering system is like a roadmap secret code. Odd-numbered highways mostly go north to south, while even-numbered ones generally run east to west. Three-digit highways have a symbiotic relationship with the main highway they share numbers with. If a three-digit highway begins with an odd number, it signals a spur route, a short journey off the main highway (eg. I-95 and 395). If the three-digit highway starts with an even number then it signals a loop or bypass leading back to the main highway (e.g. I-95 and 495). The main east-west highways go from I-10 in the south to I-90 in the north. The main north-south highways go from I-5 on the west coast to I-95 on the east coast. The highway mile markers ascend from south to north and from west to east, same as the highway numbers.
Learning to navigate high-wind conditions
High winds pose a formidable challenge when towing a trailer with a semi-truck. The expansive surface area of the trailer becomes a sail catching the wind, making steering a constant battle and being blown over a real possibility. I use the following wind guide when necessary.
I also use the Windfinder.com app to determine wind levels for my location.
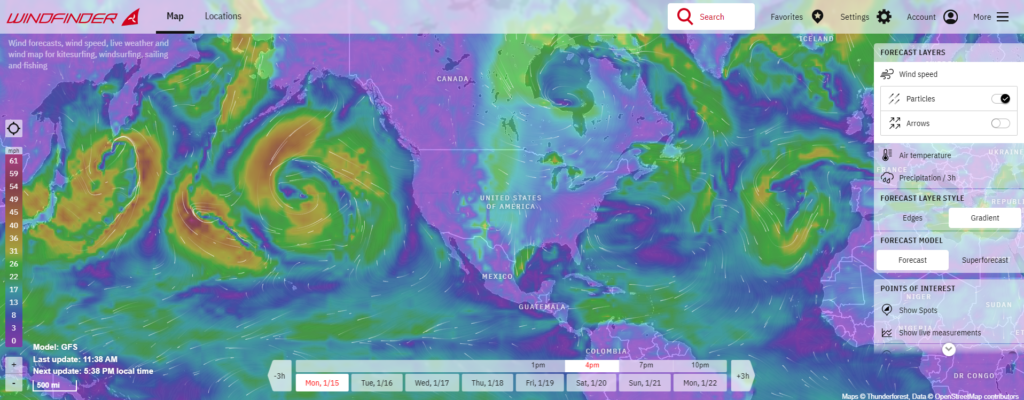
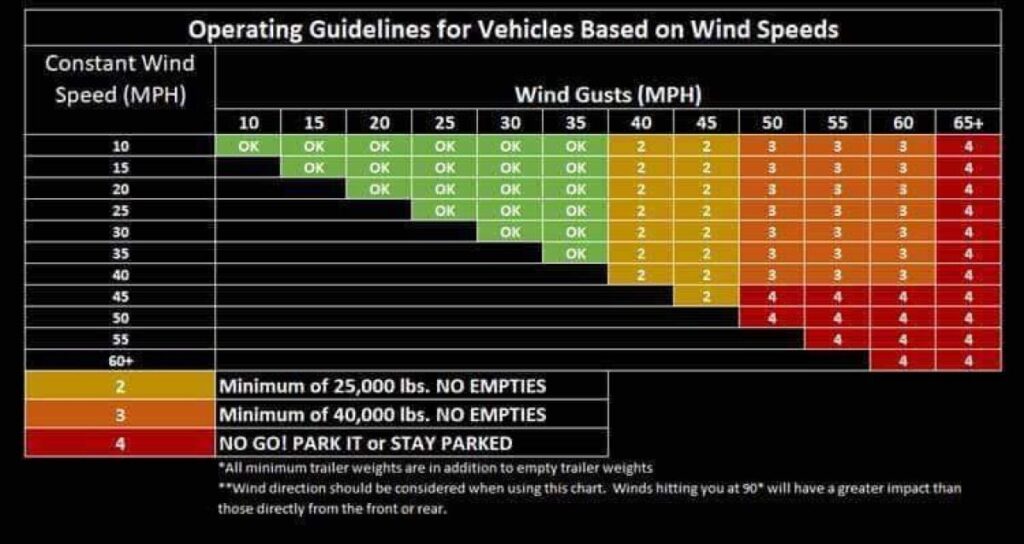
Learning to use weather tools
I mostly pay attention to two types of news–weather and traffic. For checking the weather for my drives I use an app called RadarNow (https://radarnow.org/)
Learning to use each state’s traffic and road conditions tools
During winter travels, specific state apps become indispensable, and I regularly use those of California, Washington, Oregon, Wyoming, and Nevada to stay informed and ensure a smooth journey. Also, here is a link to the National Weather Service website that provides phone numbers and links to each state’s website for checking traffic conditions. https://www.weather.gov/cys/unitedstatesroadconditions
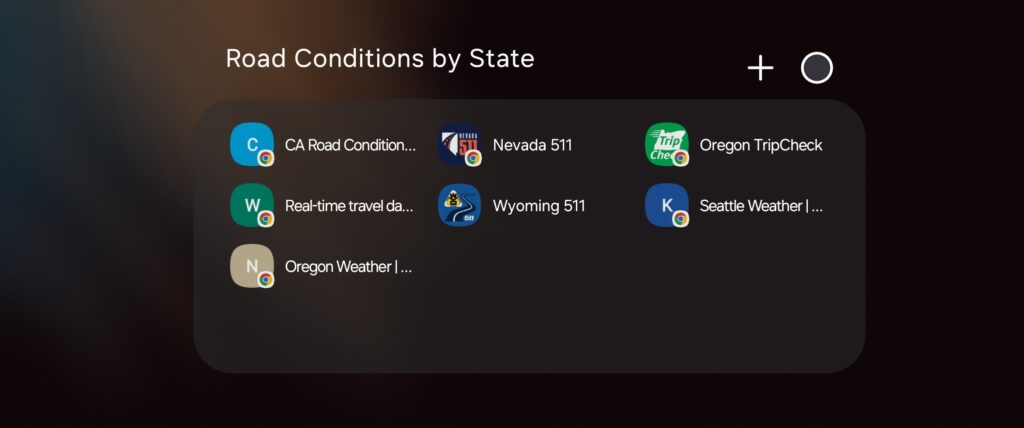
Element Two: Learn Truck Maintenance (Or in My Case, Preventative Maintenance)
Maintaining the truck is the second essential skill needed to truck profitably. Maintenance is my Achilles’ heel among the essential trucking skills, and I advocate for investing in learning basic repairs if you have the knack and inclination. However, my workaround involves an unwavering commitment to preventative maintenance. My initial truck and trailer were pre-loved, exposing me to a myriad of issues and teaching me the art of foreseeing and preventing potential headaches.
Truck Preventative Maintenance Techniques
Of the headaches I mentioned that were related to the truck, many were due to problems with the engine and exhaust system, so many of the following techniques focus on preserving those systems.
- Drive 55 to 58 mph – increases my fuel mileage and decreases wear on the engine for the same amount of miles driven.
- No idling – keeps my engine hours down. A mechanic told me that the heating and cooling–and thus expansion and contraction–of the metals is a contributor to the wear of these systems over time. Thus any lessening of this process can help preserve them.
- Extending landing gear when getting loaded and unloaded – We have all felt how jarring it can be when the forklift is bouncing around in the back of the trailer. If it feels that jarring inside of the cab, it must be putting a strain on our drive axles. If you get loaded and unloaded each once a day with 20 pallets, then that is a forklift rumbling across your floor 80 times a day (in and back out). That’s 560 times a week that the forklift is putting stress on your trailer axles and drive axles. It’s unavoidable for the trailer axles, but you can avoid (or at least lessen) it on the truck axles by putting your landing gear down and dropping your airbags.
Trailer Preventative Maintenance Techniques
On my old trailer, someone had tried to move the tandems when the pins weren’t retracted. They did it so forcibly that they made the ring holes somewhat oval and created grooves in the pins where the metal ring had dug in. As a result, the metal holes would sit snugly in these grooves making it hard for the pins to retract. So every time I slid my tandems I would first have to slide them a half inch to get the pins centered before trying to retract the pins. Only then could I slide the tandems. Doing this every time I needed to slide the tandems was a lot of extra work.
This extra toil taught me to be careful with my trailer and now I’m very delicate when sliding my tandems. Here are some of my trailer preventative maintenance tips:
- WD-40 the four pins and the inside of the trailer rails every time before sliding my tandems.
- If possible, I slide my tandem axles when the truck is empty to avoid having to slide it when loaded. I typically put them at the 41 ft mark as that covers the majority of the states and it seems to be a nice point that balances heavy loads correctly.1
- I don’t care if it takes me a whole minute to go one foot, I try to gently tap the dock with my trailer so I barely feel it touch.
- When dropping the trailer, I make sure to leave the landing gear an inch or two off the ground and lower them to the ground by dropping the airbags. After I am loaded, raising the airbags takes the weight off of the legs and the crank is much easier to turn. This way I don’t end up bending or breaking my crank handle when a heavy load makes it hard to turn.
- Once when I went under a bridge that was only just high enough for the trailer I got out and used a measuring stick to reach up and see how high it was. Now I know that at the limit of my reach if the measurement stick says 75in. then I can pass through safely.
All in all, when it comes to preventative maintenance, I think I just do a lot of little things that all add up in the end.
Element Three: Learn to Do Accounting
When I first came into trucking, I initially thought that it would be a sort of sabbatical. I would take some time off from my career, travel the country, and come back to my profession refreshed and rejuvenated. To this end, to make my trucking time productive, I enrolled in an online accounting course and began completing the coursework at night in the truck stops after shutting down for the day. I didn’t realize it at the time, but I was preparing for when I would be both a truck driver and business owner and need to find the time to manage my business from the road. The accounting courses I took also prepared me for this future role. Of all the things I learned, I think the most important for trucking is understanding fixed and variable costs. Learning to track my costs has helped me make better business decisions while trucking. I track my costs using a spreadsheet I created. Here is a copy for anyone who doesn’t already have one or would like to use the same one I use.
When I had about 4 months remaining to complete my accounting program, I left Knight Transportation to work on the course full-time. I completed the course in London during the COVID-19 lockdown and afterward returned home looking to find a new job.
Element Four: Learn to Do Taxes
Back home from the UK, I got a customer service job at the IRS helping taxpayers figure out their taxes. Of the many of us hired, most chose to work from home and only I and another guy chose to work in the office. He was soon fired for checking his own account and so I had this huge customer service floor all to myself as my personal office. Talk about stark contrast to the confined workspace of a semi-truck! With no one around to listen in, I didn’t care how long my calls took and I proceeded to give people the best customer service they could ever hope to receive from an IRS phone employee. If you happened to get me you were truly lucky and they were so grateful for the unexpected compassionate help I offered. Some of them even earnestly invited me to visit them and their families when I returned to trucking. Anyway, I digress. I just really enjoyed helping them so wanted to mention it.
Transitioning to tax management, doing your taxes is the final tool in the trucking owner’s toolbox. Beyond the obvious benefit of saving money on professional services, handling your taxes personally offers the unique advantage of having the business expert (you) also be the one filing. I have a theory that I would rather have an average mechanic who truly cares about getting the work done right than an expert who doesn’t. I think the same principle applies to doing your own taxes.
The reasonable salary I claimed during my first three years as a trucking business owner
One perplexing area is determining a reasonable salary S-corp owners should pay oneself.2 Online resources present various hypotheses, creating an air of mystery around this topic. While I am not providing tax advice, I’ll share my approach to the reasonable salary issue in my three years as a trucking company owner.
- Year One – Starting operations in July with 6 months of trucking and 5 months of IRS salary, I opted not to pay myself any salary, considering both that I already had a salary to claim and the initial phase of a new business.
- Year two- I established and funded my solo 401k. I also invested in some I-bonds. As an S-corp, I am able to invest funds both personally and as a business. For all of the funds I invested personally, I had to have a corresponding salary amount. So at a minimum, I paid myself a reasonable salary of the amounts that I had invested.
- Year Three – No salary is claimed for a couple of reasons. First, after depreciating my new truck purchase, my business income is negative for the year, justifying no salary. Second, having ‘gone all in’ on trucking with no personal expenses, I claim zero salary in the absence of owner draws and personal salary requirements.
Conclusion
The four essential elements you will need to successfully run your own trucking company are being able to drive the truck, maintain the truck, keep up with your business accounting, and do your taxes. I did not plan ahead for owning my own trucking company. However, in retrospect, I managed to set myself up darn near perfectly by learning three of these skills along the way. The only thing I could have improved was taking a diesel mechanics course or two. But even without the maintenance piece, I have been able to operate very successfully. This realization underscores a crucial point—perfection in every aspect is not a prerequisite for owning a successful trucking company. So lake that leap to freedom!
- Many states, not just Florida, have regulations specifying that trailer axles should be within 41 feet.
↩︎ - In the context of trucking entrepreneurship, an S-Corporation (S-Corp) is a legal structure that allows business owners to enjoy certain tax benefits. When considering a reasonable salary, S-Corp owners must determine a fair and justifiable amount to pay themselves for their roles within the company. This decision involves balancing business profitability, industry standards, and compliance with tax regulations. It’s important to consult with a tax professional for personalized advice on establishing a reasonable salary based on individual circumstances and applicable tax laws. ↩︎